www.industriogteknik.com
18
'17
Written on Modified on
Praktisk tilgang til at styre spild i produktionen
Producenter forsøger hele tiden at finde måder, hvorpå de kan maksimere produktiviteten og effektiviteten. I dag omfatter disse bestræbelser ofte højteknologiske programmer, der beskæftiger sig med buzzwords som cloud, datadrevet produktion, cyberfysiske systemer og Industri 4.0. Disse avancerede initiativer er fremragende koncepter og kan skabe imponerende resultater. Virkelighedens produktion kolliderer dog ofte med implementeringen af sådanne ambitiøse planer, og en kritisk virkelighed af ukontrolleret spild i fremstillingsprocessen. Inden digitalisering og optimering kommer på tale, skal producenten undersøge sine operationer, finde ud af, hvor der opstår spild og udvikle metoder til at reducere eller helt fjerne spildet. Styring af spild er det første skridt hen imod at forberede en virksomhed på indførelsen af avancerede intelligente produktionsstrategier. Figur 1 – Totalt overblik over alle elementer, og hvordan de relaterer og interagerer med hinanden i et produktionsanlæg (NÆSTE TRIN-model og -koncept).
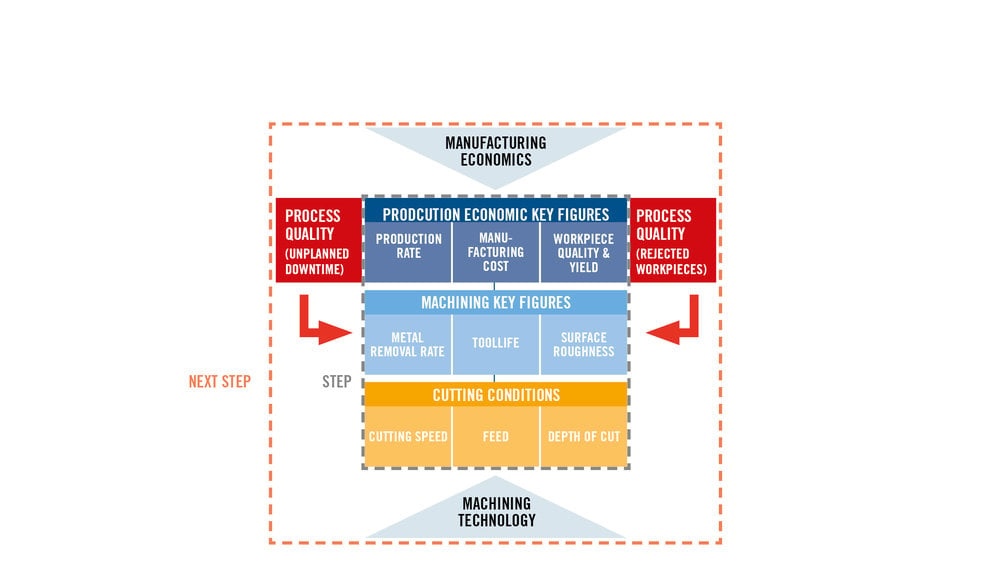
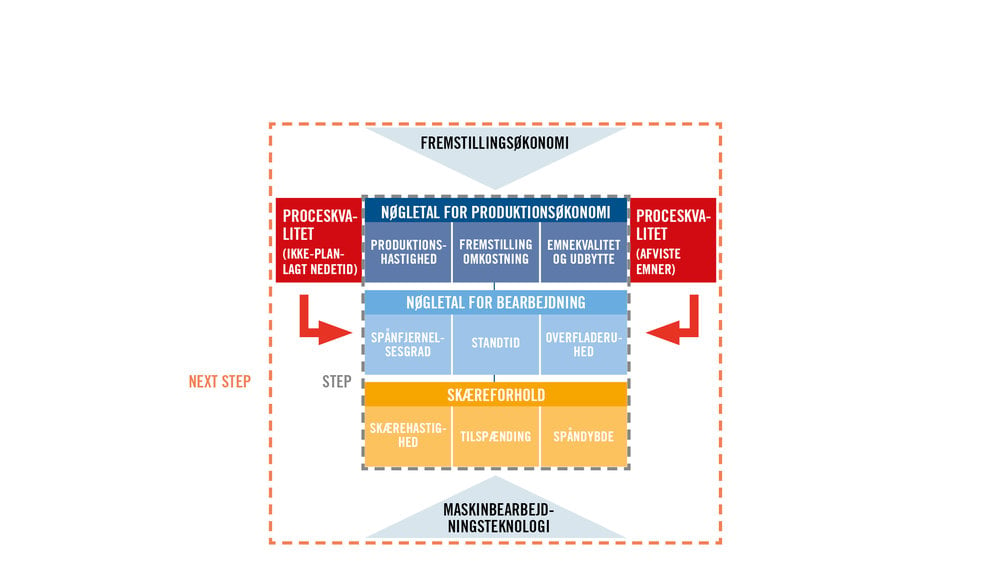
Grundlæggende produktionsøkonomi
Fremstilling består af en lang række omdannelsesprocesser. Et værksted former råmaterialer til færdige eller halvfærdige arbejdsemner gennem en række individuelle omdannelsesaktiviteter såsom smedning, svejsning eller maskinbearbejdning. Et antal individuelle elementer udgør den enkelte aktivitet. De grundlæggende elementer i maskinbearbejdning omfatter f.eks. skæreværktøj, maskinværktøj, opspændingsværktøjer og kølemiddeltilførsel. Tilsammen danner disse elementer et bearbejdningssystem, som understøttes af tilhørende udstyr og komponenter i et produktionssystem.
Planlægning, programmering og økonomistyringsfunktioner omgiver produktionssystemet og danner et produktionsmiljø. Det vigtigste element i et produktionsmiljø er mennesker. Selvom produktionen i dag i stor udstrækning benytter computere, robotter og anden avanceret teknologi, tager mennesker beslutninger, der overordnet styrer miljøet.
Maskinbearbejdningsprocessen er baseret på tekniske applikationsoplysninger med hensyn til værktøjsudvælgelse, skæreforhold, programmering og arbejdsemnemateriale og opspændingsværktøjer. Andre vigtige oplysninger omfatter produktionsmængdekrav og den angivne kvalitet af færdige arbejdsemner.
Når tekniske applikationsoplysninger sammenholdes med økonomiske overvejelser, kaldes det produktionsøkonomi. Målet med videnskaben om produktionsøkonomi er at afbalancere alle involverede faktorer. Mens tekniske elementer skaber de ønskede resultater i form af arbejdsemnekvalitet, kvantitet og rettidighed, skal aktiviteterne udføres til en omkostning, der gør virksomheden rentabel.
Balancen mellem produktionsresultat og omkostninger inden for bearbejdningsprocesser opnås gennem tre faser. Den første fase er etableringen af en driftssikker bearbejdningsproces. Det er af afgørende betydning, at antallet af uventede hændelser, såsom ødelagte værktøjer, ukontrollerede spåner og deraf følgende ødelagte arbejdsemner, minimeres. Et værksted opnår driftssikkerhed ved at vælge værktøjer med en belastningskapacitet, der opfylder eller overstiger de mekaniske, termiske, kemiske og tribologiske belastninger, der dannes i bearbejdningsprocessen.
Figur 2 – Total bearbejdelighedsmodel udarbejdet i STEP.
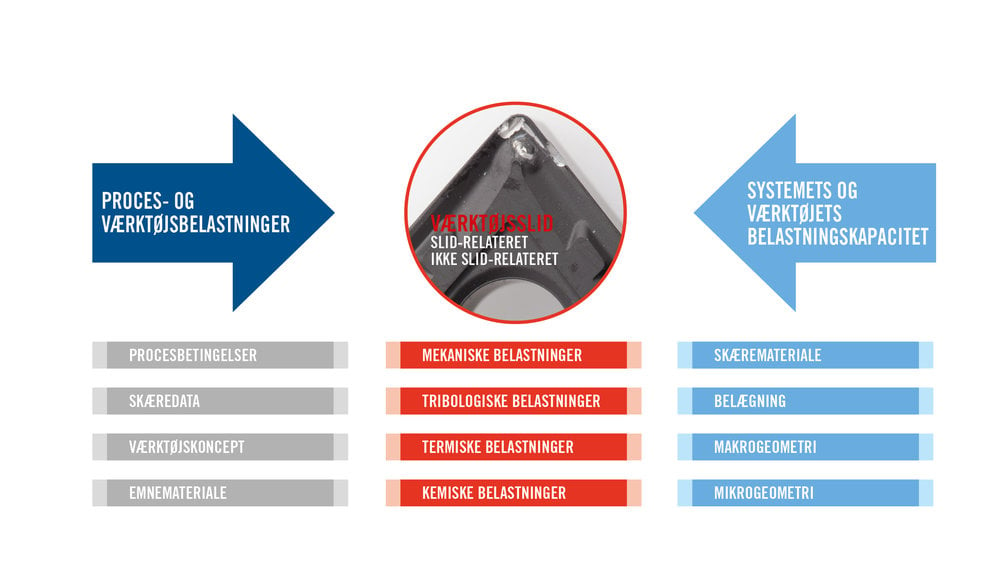
HQ_ILL_Machinability _model
Fase to i at opnå en balanceret produktionsøkonomi omfatter valget af skæreforhold, der afspejler de begrænsninger, der findes i den virkelige verdens bearbejdningsprocess. De teoretiske muligheder i et skæreværktøj er omfattende. Men værkstedets virkelighed begrænser omfanget af effektive applikationsparametre.
Et værktøjs egenskaber og ydeevne kan således variere i forhold til kraften, emnematerialet, eller konfigurationen af en del, der kan være tilbøjelig til at vibrere eller blive forvrænget. Selvom der er et stort udvalg af skæreforhold, som vil fungere i teorien, indskrænkes omfanget af et problemfrit valg desværre af virkelighedens begrænsninger.
Figur 3 viser et stort udvalg eller antal af skærehastigheder, spåndybder og tilspændinger, der er indsnævret til et mindre udvalg og en reduceret mængde som anerkendelse af forskellige virkelighedssituationer med en specifik skæreapplikation.
Figur 3 – 3D-visning, der viser samlingen af alle kombinationer af skæreforhold, som kan anvendes inden for begrænsninger forårsaget af skæremiljøet.
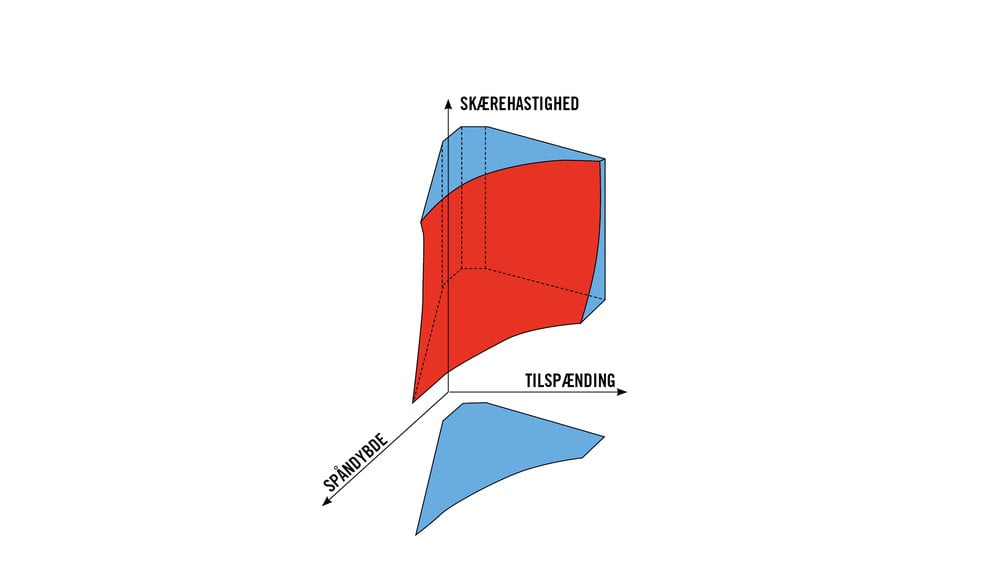
HQ_ILL_Machining_Process_cutting_conditions
Ved at anvende skæreforhold, der ligger uden for applikationsbegrænsningerne i den specifikke situation, opnås negative økonomiske konsekvenser, herunder højere omkostninger og en lavere produktivitet. Måske er 90% af de problemer, der opstår under bearbejdning, et resultat af manglende respekt for de begrænsninger, som værkstederne tillægger skæreprocessen.
Når skæreforholdene ikke overstiger de begrænsninger, der lægges på virkelighedens værksted, er aktiviteten sikker ud fra et teknisk perspektiv. Det er dog ikke alle teknisk sikre kombinationer af skæreforhold, der skaber samme økonomiske resultat. Ændringer i skæreforhold ændrer omkostningen ved bearbejdningsprocessen. Ved at overgå til mere aggressive, men stadig teknisk sikre skæreforhold, øges produktionen af færdige emner. Men efter et bestemt punkt falder produktionen, fordi de aggressive skæreparametre samtidig resulterer i en kortere standtid. Produktionen af dele falder således med tiden, fordi der bruges mere tid på at skifte nedslidte værktøjer.
Der er en kombination af skæreforhold, som resulterer i en balance mellem produktionsmængde og produktionsomkostninger. Figur 4 viser forholdet mellem skæreforhold, produktivitet og værktøj og maskinomkostninger. (Grafen er udelukkende baseret på elementer, der varierer, så længe skæreforholdene ændrer sig – materiale, ekstraarbejde og administration samt konstruktionsomkostninger er ikke indregnet.) Mere aggressive forhold ses til højre på akserne og højere produktivitet ses øverst. Det lyseblå bånd midt på grafen angiver, hvor skæreforholdene skaber en afbalanceret blanding af produktivitet (størst muligt udbytte) og økonomi (laveste omkostning).
Figur 4 – forholdet mellem skæreforhold, produktivitet og bearbejdningsomkostninger. Denne figur viser en forenklet model, som ikke medregner spildfaktorer.
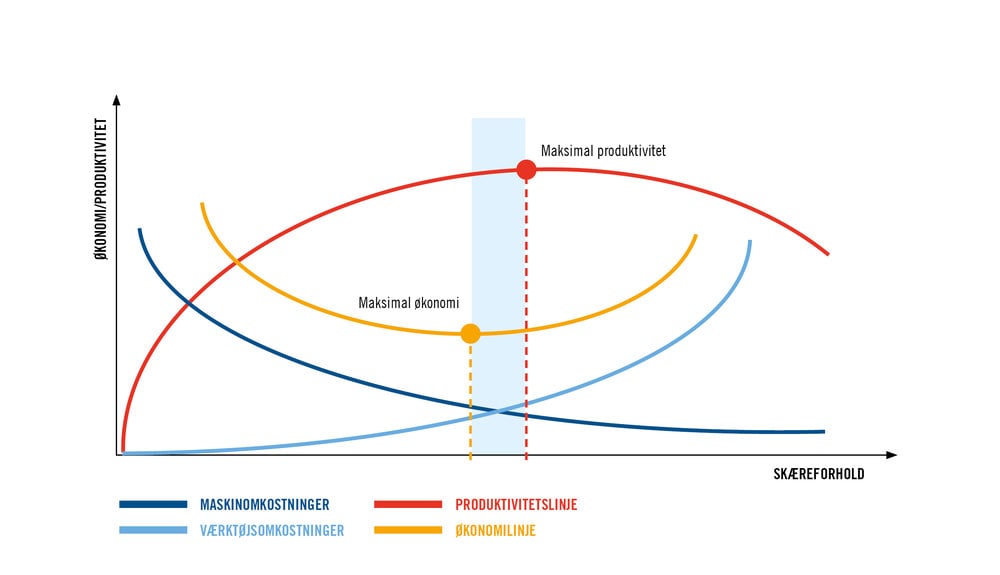
HQ_ILL_Machining_Process_relationship_cutting_conditions_productivity_machining_costs
Som følge deraf omfatter den tredje fase, som handler om at opnå en balanceret produktionsøkonomi, fastlæggelsen af den optimale kombination at skæreforhold i en given situation. Det er vigtigt at tage højde for alle faktorer i bearbejdningsaktiviteten for at kunne skabe et arbejdsdomæne, hvor skæreparametrene giver de ønskede produktivitetsmæssige og økonomiske niveauer.
Spilds indvirkning på produktionsøkonomien
De elegante videnskabelige metoder til at opnå en balanceret produktionsøkonomi afhænger desværre af mængden af spild i produktionssystemet. Spild ødelægger balancen og opstår på mange måder. Det er f.eks. spild af energi og strøm, når et 60 kW maskinværktøj anvendes i en fortløbende applikation, der blot kræver 15 kW. Når færdige emner i en anden situation ikke opfylder de nødvendige kvalitetsniveauer, går tid, penge og ressourcer, der investeres i processen, til spilde i jagten på at nå et uacceptabelt resultat. På samme måde er det et spild, når der fremstilles emner, som unødigt overstiger de påkrævede kvalitetsniveauer, idet opnåelsen af en øget kvalitet øger omkostningerne.
En mindre indlysende og mindre forstået anledning til spild er manglende eller forkert brug af intellektuelle ressourcer. Visse medarbejdere i en virksomhed kan have en viden eller kompetencer, som medvirker til at opnå virksomhedens mål, men af årsager lige fra dårlig kommunikation til virksomhedens interne politik deles viden og kompetencer ikke og går således til spilde.
Værktøjer til at reducere spild
Efter spild er blevet identificeret og kategoriseret, bør et værksted udarbejde en plan for at begrænse eller helt fjerne det. Der findes en lang række værktøjer, der gør en producent i stand til at lokalisere, kvantificere og minimere uøkonomiske rutiner. En analyse af værktøjsanvendelse, -manipulation og -forringelse udpeger f.eks. problemområder.
Disse analyser har vist, at helt op til 20 til 30 procent af værktøjer, som personalet havde defineret som slidte, i nogle tilfælde faktisk stadig var tjenlige – den resterende standtid var gået til spilde. Etablering af tydelige kriterier for værktøjsslid og viderekommunikering af standarder til værkstedspersonalet, mindsker spild af standtid betydeligt.
På samme måde kvantificerer analyser af maskiners nedetid, der bruges på aktiviteter som opsætning, programmering og værktøjsskift. Disse analyser indikerer ofte at op til 50-60% af maskiners nedetid kan undgås gennem en bedre forståelse, udførelse og koordinering af disse nødvendige, men tidskrævende aktiviteter.
Brug af interviews, undersøgelser og uddannelsesprogrammer kan afdække mange nyttige oplysninger, når det handler om personaleproblemer, der fører til spild af intellektuelle ressourcer samt ikke realiseret viden og kompetence. Som et resultat deraf udfører medarbejderne deres job bedre og opbygger evner, som maksimerer personalets produktivitet.
Styring af værdiskabelse, værdiaktivering og unødvendige aktiviteter
I begyndelsen af det 20. århundrede undersøgte den amerikanske industriingeniør, Fredrick Taylor, værkstedsoperationer og foreslog, at produktivitetsforbedringer bør drives ved at fjerne aktiviteter i en proces, som ikke tilføjer værdi til slutproduktet. Moderne “lean”-produktionsvejledninger følger den samme tankegang.
I bearbejdningsoperationer opstår den eneste sande værdiskabende aktivitet, når værktøjet rent faktisk skærer metal og producerer spån. Andre handlinger som f.eks. indspænding og opspænding, der er værdiaktiverende aktiviteter, tilføjer ikke direkte værdi til det fremstillede produkt, men kræves for at den værdiskabende aktivitet opstår.
En tredje gruppe af aktiviteter inden for bearbejdningssystemer er dem, som ikke er nødvendige. Disse aktiviteter skaber hverken værdi eller muliggør skabelsen af en værdi, men forbruger i stedet ressourcer uden et reelt udbytte. De er udelukkende anledninger til spild. Problemløsning er et eksempel på en unødvendig aktivitet. Hvis en proces udformes og styres korrekt første gang, opstår der ikke problemer, og der spildes ingen tid med at løse dem.
Figur 5 – Skematisk billede af et bearbejdningsværksted og alle dertil knyttede elementer.
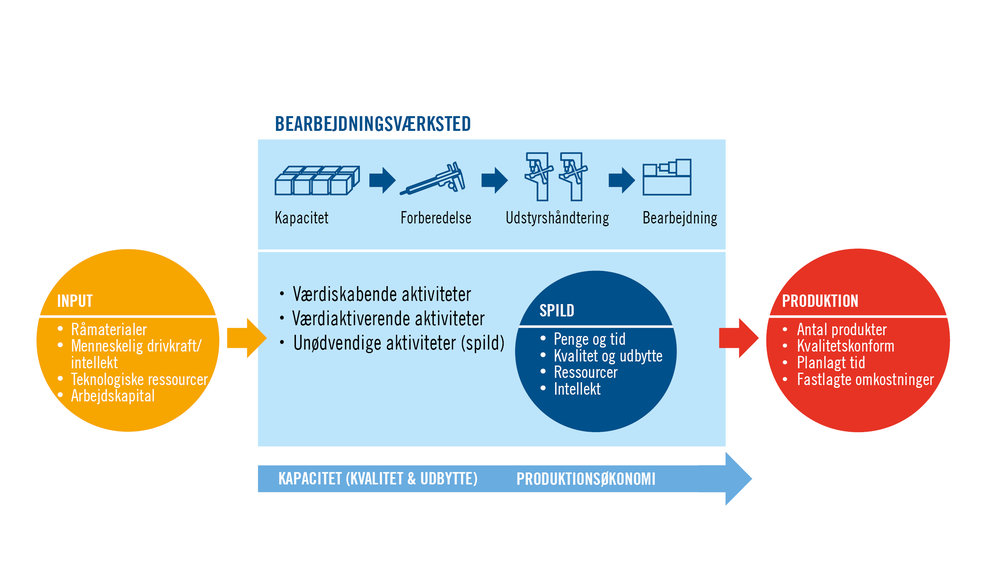
HQ_ILL_Machining_process_workshop
Konklusion
I fortiden accepteredes meget unødvendige aktiviteter som en del af fremstillingsprocessen og ansås ikke som betydelige forstyrrelser i opnåelsen af en balanceret produktionsøkonomi. I vore dage vender opmærksomheden sig mod fjernelsen eller minimeringen af unødvendige aktiviteter. Inden for produktivitets- og kapacitetsplanlægning fokuseres der på at fjerne unødvendige aktiviteter, minimere værdiaktiverende aktiviteter og optimere værdiskabende aktiviteter. (Se figur 6)
Figur 6 – Oversigt over værdiskabende aktiviteter (orange), værdiaktiverende aktiviteter (blå) og spildaktiviteter (rød). Medarbejderfaktoren (grå) er den vigtigste faktor i den optimale opnåelse af de bedst mulige produktionsresultater.
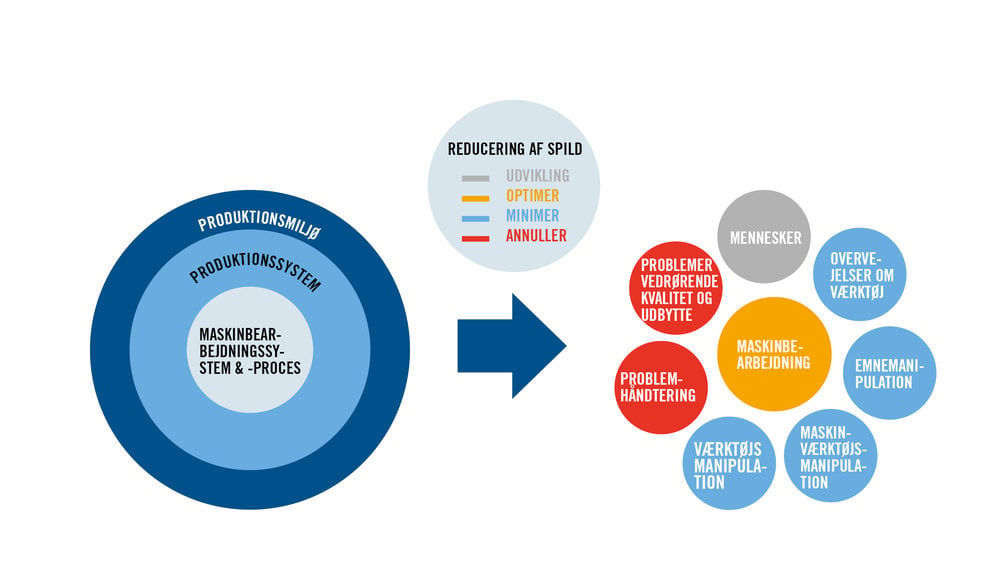
HQ_ILL_Machining_system_process
Når spild elimineres, bliver teoretisk produktionsøkonomi til praktisk produktionsøkonomi. På det tidspunkt kan fremdriften i produktionsøkonomien overføres direkte til virksomhedens succes. I bestræbelserne på at fjerne alle anledninger til spild er det nødvendigt at udvise forsigtighed. Det er vigtigt at kvantificere afkastet ved spildreducerende aktiviteter. Helt at fjerne en bestemt forekomst af spild kan medføre en investering, der er så stor, at det ud fra et økonomisk perspektiv kunne være bedre at acceptere spildet, eller en del af det, og leve med det. Sådanne beslutninger træffes efter en passende kvantitativ analyse samt drøftelser internt i virksomheden om, hvordan beslutningerne påvirker virksomhedens mål og filosofier.
Underartikel:
Secos rådgivningstjenester
Da fremstillingsprodukter bliver mere avancerede, skal brugere øge mængden af applikationsassistance for at realisere maksimal fordel af de nye teknologier. Inden for bearbejdning er det indledende assistanceniveau en rettesnor i valget af det rigtige værktøj til en bestemt aktivitet. Efter et værktøj er valgt, danner yderligere oplysninger grundlag for valget af optimale skæreforhold, brug af kølemiddel og andre overvejelser. Hvis et værktøj derefter ikke fungerer som forventet til den aktivitet, kan værktøjsleverandøren yde hjælp til fejlfinding. Disse tre former for assistance udgør traditionelle værktøjstjenester.
Når værktøjstjenesten udvides fra en enkelt applikation til også at dække en proces, hvor et emne udsættes for flere operationer på én eller flere maskiner, skal slutbrugere have vejledning i opsætning af rækkefølgen af aktiviteter, emnemanipulation og andre faktorer for at maksimere effektiviteten og produktiviteten. Dette assistanceniveau kan kaldes konstruktionstjenester.
Oftere og oftere søger producenter vejledning i at forbedre funktioner, produktion og omkostningsstyring for et helt værksted eller en hel organisation. I disse tilfælde gennemfører nogle uafhængige konsulentvirksomheder det, de beskriver som styring eller produktionsrådgivning. For at gennemføre en gennemgående vurdering af en produktionsorganisation, er det dog af afgørende betydning, at man fuldt ud forstår virksomhedens kerneaktivititeter.
Med sin lange og omfattende erfaring i at opnå forståelse for bearbejdningsprocesser og -værktøj har Seco i årtier leveret traditionelle værktøjstjenester, konstruktionstjenester og i et vist omfang rådgivning i et større perspektiv. Disse ydelser blev tilbudt på en betinget eller situationsspecifik basis, men i 2016 dannede Seco Consulting Services for at give sine kunder et mere strømlinet og responsivt udvalg af fremstillingstjenester.
Seco Consulting Services omfatter en lang række specifikke ressourcer og leveringsmetoder. Værktøjsudvælgelse og applikationsassistance er tilgængelige online hele døgnet for at imødekomme øjeblikkelige produktivitetsbehov på værkstedet.
Konstruktionstjenester kan begynde med elektronisk kommunikation og kan udvides til besøg på stedet, hvis behovet skulle opstå. Seco Consulting Services inkluderer ligeledes omfattende analyse og vejledning, der involverer betjeningen af hver eneste funktion i et værksted. Disse tjenester kan omfatte rådgivning om vedligeholdelse af maskinværktøj, udformning af værkstedet, logistik og organisationsmæssige funktioner. Rådgivning om personalekompetencer og spørgsmål om vidensdeling samt forhold i forbindelse med fremstillingsteknikker, der anvendes i virksomhedens produktionsstrategier og omkostningsovervejelser kan ligeledes inkluderes.
Hvert eneste Seco-rådgivningsforhold er baseret på NEXT STEP-konceptet, men kan også skræddersys til den deltagende virksomheds specifikke behov, og består af en dialog mellem Seco og kunden med fokus på at opnå et fælles mål.